责任编辑:
lxy
时间:2024-02-28
来源:转载于:技术邻CAE学习
责任编辑:
lxy
时间:2024-02-28
来源:转载于:技术邻CAE学习
1 概述
汽车在加速、减速、转弯、上下震荡等情况下,蓄电池装置会随之运动,因此,固定蓄电池装置的蓄电池支架强度和刚度必须满足要求,以保证蓄电池为汽车正常行驶及车内电子系统正常运行供电。考虑到蓄电池支架的注塑工艺性以及蓄电池支架在发动机舱的存放空间,蓄电池支架的结构设计与分析势在必行。
本文借助HyperMesh中的OptiStruct求解器,运用材料线性和分析性有限元仿真分析方法,主要考虑蓄电池朝整车方向加速运动时,在产品设计阶段对某车型的蓄电池支架进行强度分析,从而发现蓄电池支架薄弱地方,根据分析结果对支架结构进行优化。
2 有限元模型的建立
2.1 几何模型的建立
蓄电池支架装配体原始几何模型如图1所示,为了提高计算精度及计算效率,需简化原始几何模型,简化后的蓄电池支架装配体如图2所示。
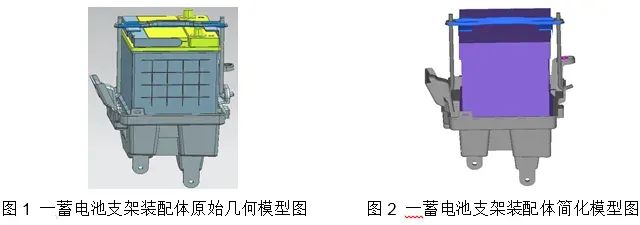
2.2 网格划分
根据模拟计算的精度要求,蓄电池支架采用四面体单元进行网格划分,单元尺寸为2mm,单元数为578626;其余部件采用六面体单元进行网格划分,蓄电池支架单元尺寸为10mm,其余部件单元尺寸均为2mm。
2.3 材料与属性
计算中所使用的材料参数见表1,长度单位为:mm。蓄电池支架应力-应变关系曲线如图3所示。
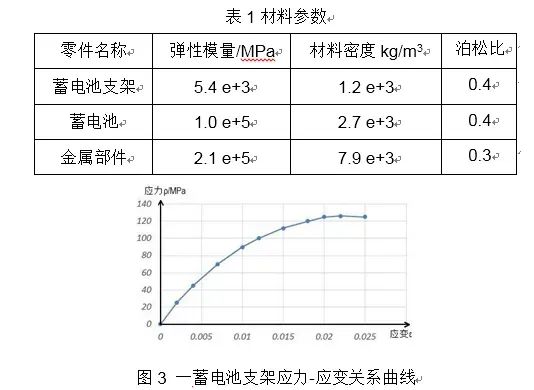
2.4 蓄电池支架有限元模型受力和约束图
为了提高计算效率与时间,将蓄电池朝整车方向的加速度转换为加载到蓄电池质心的惯性力,螺栓直径M8,等级8.8级,支架7个定位孔固定约束,如图4所示。考虑到蓄电池支架拉杆孔强度要求,对蓄电池支架拉杆孔不断改进,最终使其满足强度要求,如图5所示。运用材料线性与非线性两种方法对蓄电池支架进行对比分析,分析工况如下所示:
工况一:蓄电池以5g加速度朝整车-Z方向加速运动(g为重力加速度,单位为m/s2)。
工况二:蓄电池以5g加速度朝整车+X方向加速运动。
工况三:蓄电池以5g加速度朝整车+Y方向加速运动。
工况四:蓄电池以5g加速度朝整车-Z和+X方向加速运动。
工况五:蓄电池以5g加速度朝整车-Z和+Y方向加速运动。
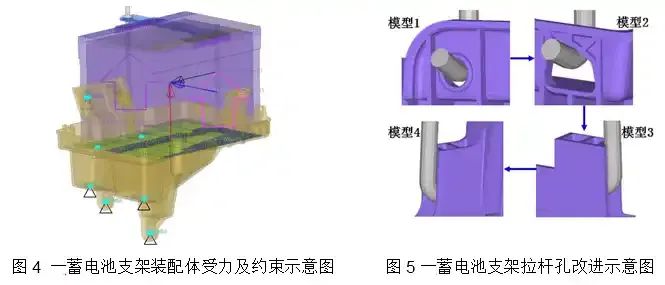
2.5 有限元模型的建立
各个部件表面之间的摩擦系数设定为0.2,有限元模型如图6所示。
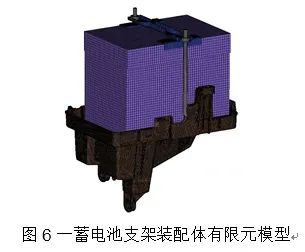
3 计算结果图
3.1 材料线性与非线性对比分析
由于材料非线性计算的时间非常长,所有仅选择模型2和模型3进行材料线性与非线性对比分析,工况四及材料非线性条件下,支架最大应力云图如图7所示,对比分析结果如图8所示。
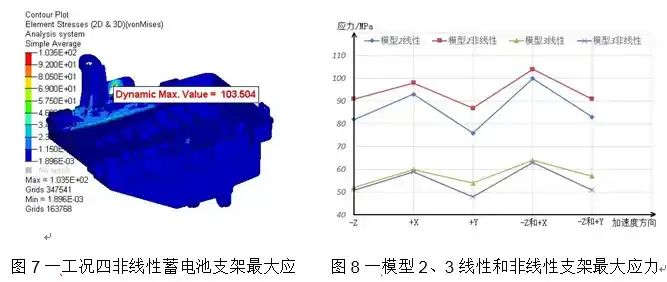
由图8可以看出:蓄电池支架在材料线性与非线性条件下的最大应力相差不大,平均相差6.7%。但是材料非线性求解时间为线性求解时间的120倍左右,因此,为了节约时间,提高效率,蓄电池支架可用材料线性求解即可。
3.2 蓄电池支架拉杆孔改进方案
对蓄电池支架拉杆孔不断改进,共设计出4种支架模型,如图5所示。工况四及材料线性条件下,支架最大应力云图如图9所示,线性条件不同支架模型结果如图10所示。
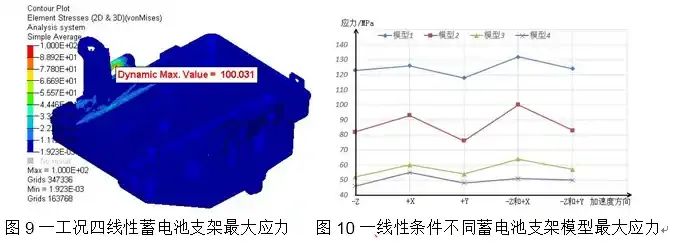
蓄电池支架拉伸强度为126MPa,取安全系数1.5。由图10可以看出:模型1、2蓄电池支架最大应力均已超出其拉伸强度126Mpa/1.5=84MPa,模型3、4满足强度要求,模型4为最优方案。
4 分析与结论
运用HyperMesh中的OptiStruct求解器可对蓄电池支架进行线性与非线性求解,改进后的蓄电池支架可使其拉杆孔不被拉裂,为蓄电池支架注塑成型提供了依据,满足客户要求,为蓄电池支架的生产带来了巨大的价值。分析结论表明:
(1)蓄电池支架在材料线性与非线性求解条件下,支架最大应力相差仅6.7%,因此可用材料线性对蓄电池支架进行有限元分析以提高效率;
(2)蓄电池支架最大应力产生在支架拉杆孔处;
(3)通过不断改进支架拉杆孔结构,支架最大应力由132MPa降低至55MPa,满足其拉伸强度要求。